All New Machines for Waste & Recycling Industry : IN DEPTH: The Cat’s Whiskers – Three New Material Handlers
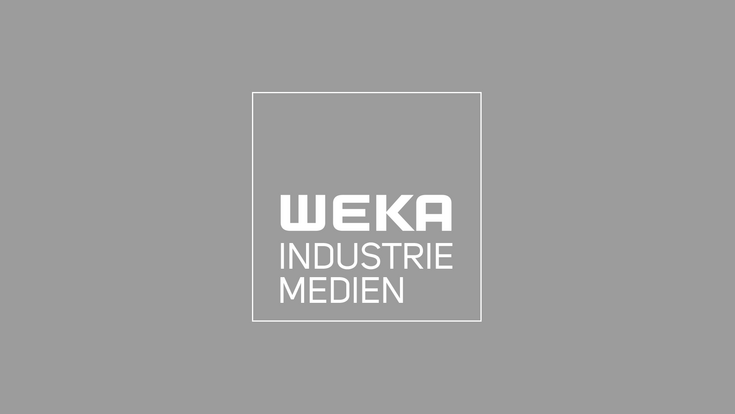
First, the bad news. The three new material handlers that I’ve come to France to see are ... Well, there’s one of each of the new models being introduced this year.
They’re brand new too. So new in fact, I’m not going to be allowed to photograph them in a real-life waste recycling facility – let alone spend the day getting them dirty. So this is no ‘hands-on’ assessment. That will hopefully come later.
My mission in Grenoble then was to have a look over the new machines, see where they will be made – and just as interesting – talk to some of the people involved with bringing the whole project together.
If the amount of money and effort that the Caterpillar Corporation has put into the production and launch of these new machines is anything to go by, they deserve to be a big success.
My visit coincided with an intensive reworking of the production facility at Grenoble, aimed at increasing efficiency and capacity at the plant. This has been made possible by moving the heavy metal fabrication out to a facility in Poland. In turn, the space that has been created is (or rather ‘was’, as this work should be completed by the time you read this) being utilised for enhanced assembly facilities.
The Grenoble plant already builds other machines including tracked ‘tractors’ and tracked loaders, many of which are used in waste and recycling applications, of course.
But aside from being able to study first hand the production lines on which the machines are built and see the care that goes into the preparing, painting and the assembly of various components that go to make up the completed machines, the really interesting part of my factory tour was seeing how the completed machines were tested before dispatch to CAT dealers and, of course, the final end-user.
It used to be done by firing up the completed machines at the end of the production line and driving them outside to the yard, where a factory-trained test driver put each machine through a test programme and ticked-off each item as the test progressed.
TESTING, TESTING
Now? Once completed, all new Cat machines are placed in purpose-built ‘Test Cells’ alongside the production lines. Each machine can now be tested – and adjusted if need be – to a consistent standard.
Why is this so important? Well, the technology isn’t replacing human input, it’s helping do more testing, more thoroughly and, of course, recording the end results more accurately, should they be needed for future reference. And why is this so important?
Well, it stands to reason, doesn’t it? More and more machines used in the waste and recycling industry are now being used inside, undercover. In fact, many will spend an entire shift – and possibly their entire working lives – inside a large shed. This is not the ‘natural environment’ for any internal combustion-engined machine.
Add dust, a build-up of heat and a constant, repetitive work cycle to the mix and there are plenty of opportunities for failure. So having the data – and being able to simulate different operational scenarios – is very useful.
So, that’s the backdrop. Now let’s take a closer look at the hardware. There are three new wheeled material handlers available this month – the ‘MH3022’, the ‘MH3024’ and the flagship ‘MH3026’. But if you’re thinking, "Three new models isn’t that impressive?"
Hang on, that’s just the start. There are indeed three new basic undercarriage, or ‘skid’ (chassis) designs, but I’ve just been looking through all the specification sheets. True, maths isn’t my best subject, but I’ve counted twenty eight different model and option permutations. Twenty Eight!
NOT TOO BIG. NOT TOO SMALL. JUST RIGHT
The ‘starter’ machine is the MH3022. This model comes with a choice of two materials-handling booms, three straight sticks with linkage and two drop-nose sticks. In his introduction, CAT product specialist Thibauld Dechamps suggested the 3022 is the ideal machine for indoor applications where operating space is tight, or where primarily lighter materials are processed.
The skid/undercarriage is 2550 mm (8 feet 4 inches) wide – making the machine both agile in plant and easier to transport by road without special permits. Operating weight is – as the model number suggests – 22,000 kg (or 21,815 to be precise).
Next up is the MH3024. There’s a longer front linkage and where greater side-stability is an issue – or because heavier materials are handled within a wider operating envelope – there is an optional 2750 mm (9 feet) wide undercarriage option.
The top-of-the-range model is the MH3026 – designed, as Thibauld Dechamps suggests, for applications where heavier, more dense materials are handled and processed.
Equipped with a long materials handling boom, there’s a choice of three drop-nose sticks ranging in length from 4.9 to 5.9 metres (16 feet 1 inch to 19 feet 3 inches) and three different undercarriage widths – only the MH3026 is available with the widest 2.99 metre (9 feet 9 inches) option.
All three basic models feature a new ‘pusher blade’ designed to help keep the worksite, or tipping f loor, clean and tidy and provide a more effective solution than the ‘traditional’ method of picking up a wad of scrap metal swarf – or an old mattress – and sweeping the surface by using the boom of the machine.
The pusher blade can also be fitted with a tow hitch. Available on all three models is the ‘Easy Cab Access Option’ – essentially a set of steps front and rear that enable the machine operator to climb up onto the skid deck (chassis) when the upper superstructure is not aligned with the undercarriage.
TALKING OF CABS
All three models feature a hydraulically-raised cab with a maximum height (ground level to driver’s eye-line) of 5170 mm (17 feet). But it’s what is on the inside that is just as important as the outside features, like the nicely-designed waste guards that swing outwards to make it easier to clean the front screen.
Or perhaps to be more accurate, it’s what is NOT on the inside of the cab that is of more interest here: ‘dust’. All three new material handlers are available with the CAT ‘Advanced Cab Filtration System’ (ACFS) as “an integrated option from the factory”, as the launch specification puts it and what I take to mean is a fully warranted factory fitted, on-line option, rather than a third party provision fitted once the basic machine has already been built.
The ACFS package is designed to “almost eliminate” dust, contaminants such as insecticides and fungus spores – and smell – from entering the cab. This is achieved by cab pressurisation. Again, like the access steps, the cab might not look revolutionary, but a unit that has been designed with doors and window seals that take into account the need for pressurisation is a far easier – and cheaper – starting point than a cab that has been designed without such a facility in mind.
A BREATH OF FRESH AIR
If preventing dust and other potentially harmful contaminants from reaching the machine operator has been one key factor in the design of these new machines, then preventing potentially harmful dust and contaminants from reaching the engine intake – and just as important, the cooling system radiators – has been an equally important mission.
After all, neither humans, nor diesel engines are designed to work in hot, dusty, indoor conditions. So alongside improving the operator’s environment, Caterpillar engineers have also put some thought into keeping dust out of the engine and cooling systems.
The air intake for both engine and hydraulic oil cooling radiators is side-mounted, high up on the superstructure and features a clever automated ‘shaker’ to prevent any initial build-up of dust before it even reaches the radiator with its axial re versing fan. Another example of good design practice? All the daily checks – and a large number of service items too – can be undertaken by the operator from ground level – a significant contribution to site safety.
The ‘Waste Handler’ package also includes new LED lighting, CCTV/ Reversing cameras and a joystick (instead of wheel) steering option, but there’s also a lot of technology aimed at getting the optimum performance out of each machine.
There’s ‘Auto Engine Speed Control’ (AESC), Automatic Engine Idle Shutdown (to prevent operators from leaving the engine running while going for a break) and an enhanced ‘Eco Mode’. Caterpillar has also gone for what is described as a ‘closed-loop swing circuit with an energy regeneration facility’. An ‘accu
mulator’ in other (rather fewer) words. This is charged during the lowering of the main boom (the accumulators sit on the boom rams) providing a potential fuel-saving hydraulic boost at the start of the next cycle.
CONCLUSION
True, there is nothing ‘revolutionary’ about these three new machines. But then ‘evolution’ is probably a far better way forward in demanding applications such as scrap, waste and recycling. The cab lift geometry has been redesigned to offer a greater feeling of stability than earlier versions.
The wide choice of undercarriage width/ boom configurations should meet just about every need. And of course there’s the level of back-up that only a major market player (like Caterpillar)
can provide. Add a new range of CATbranded tools and attachments and it’s clear Caterpillar is serious about winning a larger market share of the material handler market. Starting right now.
Thinking about it during my two hour train journey back to Geneva Airport, that is probably the main USP of these new machines – a combination of an impressive permutation of options to match what’s available from the more specialised competitors, combined with the design, production and aftercare resources that only a global player can provide.
That’s got to be a good enough reason for a closer look ...0