Carbon8 Plant to Process 50,000 TPA of Flue Gas Treatment Residues : Plant to Recycle Waste to Energy Residues into Carbon Negative Aggregates in Leeds
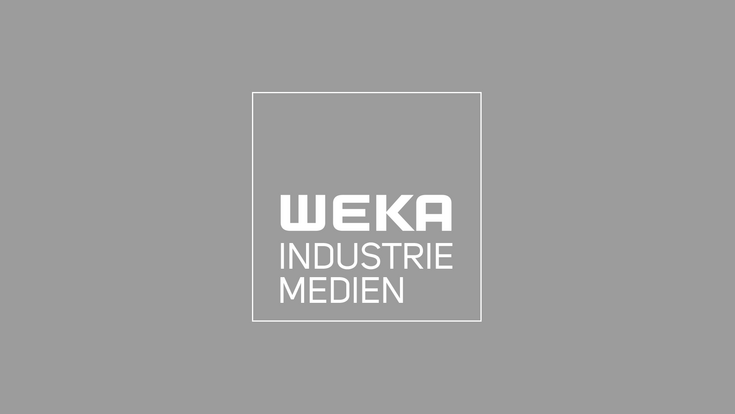
Suffolk, UK based Carbon8 Aggregates, which manufactures carbon negative aggregate materials from recycled Flue Gas Treatment residues (FGTr) from waste to energy plants, has won planning permission to build a new £4 million manufacturing facility on the outskirts of Leeds.
The joint planning application for the 13-acre site, part of an industrial estate at Cross Green to the south east of the city, was submitted with local independent building block manufacturer, Thomas Armstrong, which will build a new block production plant alongside Carbon8’s aggregate operation.
According to Carbon8 work is expected to begin on the facility in August. Once operational, the company said that the facility will create over 20 new jobs in the area and the new two-line facility will be capable of recycling 50,000 tonnes of waste to energy Flue Gas Treatment residues into approximately 110,000 tonnes of lightweight secondary aggregate.
Carbon8 added that it is well placed to benefit from the recent EU Circular Economy Package, which includes revised legislative proposals on waste to stimulate the transition to a circular economy.
It noted that a key component of the package are measures to promote reuse and stimulate industrial symbiosis – turning one industry’s by-product into another industry’s raw material.
Technology
In Carbon8’s aggregate patented manufacturing process, known as Accelerated Carbonation Technology (ACT), waste carbon dioxide gas is used as a resource to treat a wide range of thermal wastes.
The company explained that many thermal wastes react naturally with carbon dioxide, and if the reaction conditions are carefully controlled, this natural reaction can be accelerated, taking place in minutes rather than months or years and resulting in the formation of artificial limestone.
During the process, significant volumes of carbon dioxide are said to be permanently captured as stable carbonates. According to the company, the growth of the carbonates chemically stabilises and encapsulates contaminants reducing the pH of the system and locking up heavy metals.
The carbonated material is blended with binders and fillers and then pelletised with further carbon dioxide to form a rounded aggregate (C8A), which the company said has a number of applications in construction.
According to Carbon8 the resulting aggregate contains more captured carbon dioxide than released generating the energy required for its manufacture. The company claimed that this makes it the world’s first carbon negative aggregate.
Carbon8 added added that its technology will be showcased in the 2016 United Nations Environment Programme Global Environment Outlook 6 report, which is due to be published later this year.
In June 2015 the company, whose principle investor is Grundon Waste Management, secured a 10 year contract for the removal, treatment and recycling of Air Pollution Control residue from Viridor’s Exeter, Cardiff, Ardley and Peterborough waste to energy plants.
The company’s Avonmouth facility is expected to be operational imminently.
Read More
VIDEO: World First Carbon Capture & Storage at Oslo Waste to Energy Plant
A five month test program to capture carbon emissions from the municipality operated Klemetsrud waste to energy plant in Oslo, is being undertaken by Aker Solutions, a Norwegian supplier of products, systems and services to the oil and gas industry.
£110m EIB Finance for Viridor’s 30 MW Cardiff Waste to Energy Plant
The European Investment Bank (EIB) has confirmed that it is expected to provide £110 million to support Viridor’s new 30 MW waste to energy facility in Cardiff, South Wales.
World First DONG Energy Enzymatic Untreated Waste to Energy Plant for UK
Dong Energy UK is to build the world’s first commercial full-scale plant to produce biogas from untreated Municipal Solid Waste using its REnescience enzyme technology in Northwich, UK.