Six Facilities within Rouge Center Cut Landfill to Zero : Ford Achieves Zero Waste to Landfill at its Largest & Most Complex Center Yet
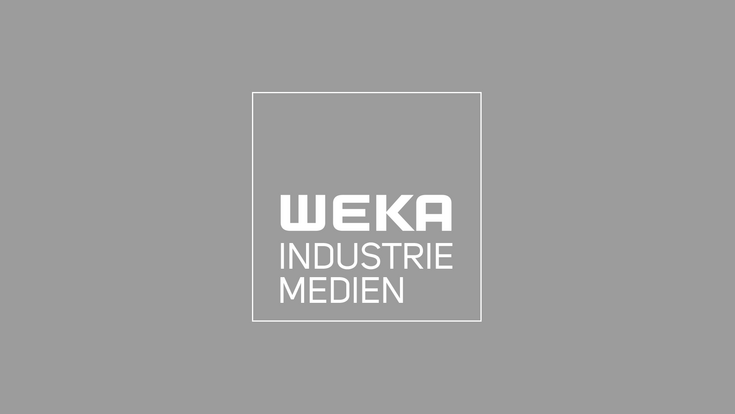
Michigan based automaker, Ford, has achieved zero waste to landfill at its historic Rouge Center in Dearborn after two years of planning.
The company said that the facility is its largest complex to send zero waste to landfill.
“With 16 million square feet of factory floor space and approximately 7,000 employees it was a challenge, but we’ve succeeded in finding solutions for our manufacturing waste streams,” said Gary Johnson, Ford North America manufacturing vice president.
The company explained that when one of its facilities is given landfill-free status, it means that absolutely no manufacturing waste from the facility goes to any landfill.
The center is now said to be keeping more than 14 million pounds (6350 tonnes) of waste out of landfills - enough to fill the beds of more than 4,400 Ford F-150 trucks.
Sustainable Model
According to Johnson since 2004, the historical Ford Rouge Center has served as the company’s model of sustainable manufacturing.
“Two years ago we instituted a closed-loop recycling system, where we recycle up to 20 million pounds (9007 tonnes) of aluminum stamping scrap each month, which is the equivalent to 30,000 F-150 bodies,” he said.
“In addition, the plant has one of the largest living roofs in the world, which helps us reduce energy usage by keeping the plant warmer in the winter and cooler in the summer,” continued Johnson.
The company added that the six facilities at the Ford Rouge Center join 68 other Ford facilities around the world in going ‘true zero waste’ to landfill.
However, t he process of diverting waste at the Rouge was said to have been a tough one because of the number of facilities there. Ford said that its environmental engineers had to look at all of the waste streams at each plant to determine what could be done with the waste.
Swarf
Ford said that one particularly difficult question was how to handle the swarf - the metal shavings and chips that are created when metal is ground during the engine manufacturing process at Dearborn Engine Plant.
The team found a machine called a briquetter that could transform the metal back into a brick that can be recycled. Any coolant oil on the metal shavings is squeezed out during the process and is then reused.
In another case, long plastic rivet strips needed to be chopped into small pieces so they could be recycled.
Importantly, Ford said that its sustainability efforts are not only good for the environment - they make good business sense.
“Our global waste strategy commits Ford to reducing waste to landfill, and we have made great progress in our facilities around the world,” said Andy Hobbs, Ford Motor Company director, Environmental Quality Office.
“We are proud of the efforts of our employees worldwide in their commitment to helping Ford reduce its global environmental footprint, and especially pleased with this achievement at our iconic Ford Rouge Center.”
Read More
Ford Looks to Make its Cars Easier to Recycle with Gecko Inspired Adhesive
Dearborn, Michigan based car maker, Ford Motor Company, is working with Procter & Gamble to develop an adhesive inspired by geckos to improve the recyclability of its cars.
New Unifi Bottle Recycling Plant Takes Recycling a Step Further
In Reidsville, North Carolina Unifi, Inc. has celebrated the opening its REPREVE® Bottle Processing Center as part of its new Plastics Recycling Facility.
Ford & Heinz Team up to Recycle Tomato Waste into Bioplastcs
Ford has teamed up with ketchup manufacturer, Heinz, to explore the possibility of recycling tomato waste into bioplastic car components.