Ennovia SARL and Crazylog Streamline Waste Maintenance Routines on Channel Island : IBM Partners Bring 'Quickbrain' Proactive Maintenance to Jersey’s Waste Department
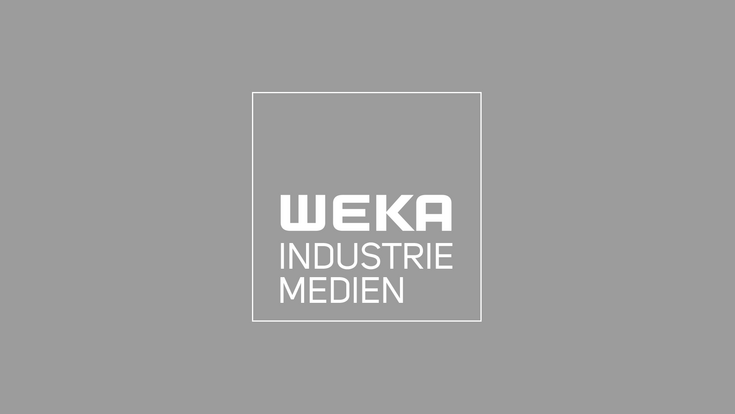
French IBM Business Partners and computerised maintenance management system (CMMS) specialists Ennovia SARL and Crazylog, have been working with the government of Jersey’s solid waste department to help it move from reactive to proactive maintenance routines of its equipment.
The Government of Jersey serves the largest of the Channel Islands, which are located off the coast of France. A British Crown dependency, Jersey has approximately 100,000 residents. The solid waste department within the government is responsible for processing approximately 75,000 tonnes of waste per year. The department includes composting facilities, reuse and recycling centres , and an energy recovery plant that converts combustible waste to electricity.
The plant’s Director, Ian Williams, wanted to find a way to improve the way the plant dealt with its equipment maintenance.
“We weren’t doing as much preventative maintenance as we needed to do, and everything was reactive,” he explained.
The plant maintained a spreadsheet that contained a list of all the equipment that needed work, but it wasn’t very searchable, and it didn’t help the facility with its goal of creating a more proactive strategy. When plant staff did take on maintenance jobs, they sometimes had difficulty locating the necessary documentation for the equipment they were working on.
“We didn’t really have a way of searching for information,” said Williams. “We had to rely on people’s knowledge, experience and memories of where we last found a document.”
After considering a couple of different maintenance management products, the solid waste department decided to work with IBM Business Partners Ennovia and Crazylog to implement its Quickbrain solution.
The waste department worked with Jean-Yves Kbaier, the Chief Executive Officer of Ennovia and Crazylog, to address the government’s security concerns. The government wanted to avoid giving third-party providers access to the government’s servers. So Kbaier suggested running the Quickbrain solution on IBM Cloud.
“Quickbrain is a web application, so it’s supplied as software as a service,” elaborated Kbaier. “And we have a long-term partnership with IBM Cloud.”
The Quickbrain product runs on IBM Cloud and the waste department can access it via a virtual private network (VPN).
Quickbrain provides modules for maintenance management, including preventative maintenance scheduling, inventory management and a record of reactive maintenance. There’s also a reporting module to help track KPIs such as the most expensive assets, the assets that cause the most downtime, and the most used spare parts.
The Quickbrain documentation module is designed to help industrial facilities better manage and access their technical documentation. To begin using it, plant staff simply dragged and dropped all of their existing documents into the Quickbrain solution.
Kbaier helped introduce the Quickbrain solution to the solid waste department slowly to help staff adjust to the new solution and processes.
“We started with simply raising a fault,” said Williams. “And we’d work for a month or so learning about that to make sure everyone knew how to raise a fault. Then we moved on to preventive maintenance. Jean-Yves was very good at making sure that people were on board with the solution.”