Success Story: Doosan Lentjes : New waste-to-energy plant in Olsztyn is essential for the disposal need in Poland
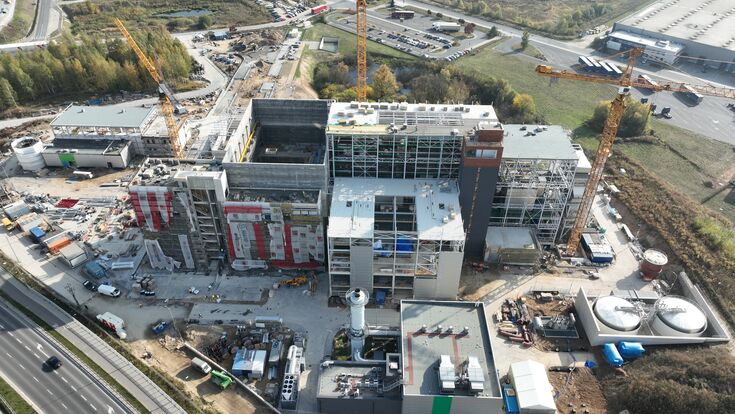
The waste volume in Poland has increased since 2010 from approximately 12.1 million tonnes per year to almost 13.1 million tonnes by 2020. It is expected that the total waste generated will stabilize at around 15 million tonnes. This of course means that the country has to quickly find ways to deal with the waste generation since – just like any other EU member – it has to fulfill the municipal waste landfill quota of 10 per cent from 2035 onwards.
The country already launched and implemented a whole series of projects in recent years. In 2007 Poland started the planning for the establishment of thermal waste management infrastructure. As of 2022 eight grate-based facilities have gone into operation with a total capacity of about 1.3 million tonnes per year. Another four waste-to-energy plants with a capacity of over 600,000 tonnes per year are currently under construction. One of them is located in Olsztyn, in the north-east of Poland.
Built with Doosan Lentjes technology
The project has been in development by the municipal district heating network company MPEC since 2012 as a public-private-partnership (PPP). The need for a new heat source in the city arose from the fact that the second largest heat source provided by the Michelin company ceased operation. So, Dobra Energia, a consortium of the French infrastructure investor Meridiam and the Spanish waste management company Urbaser, was awarded with the contract based on a concession model in 2019.
In 2020, the consortium of Doosan Lentjes and its Korean parent company Doosan Enerbility was awarded the contract by Dobra Energia as general contractor for the turnkey project, including civil works. Doosan Lentjes, as a one-stop supplier for waste-to-energy, offers interface-optimized solutions for the chute-to-stack process with its proprietary technologies for grate, steam generator and flue gas cleaning. So, for the duration of the concession, Urbaser will act as operator. And Doosan Lentjes is responsible for the design, supply, installation and commissioning of the entire electromechanical part of the plant.
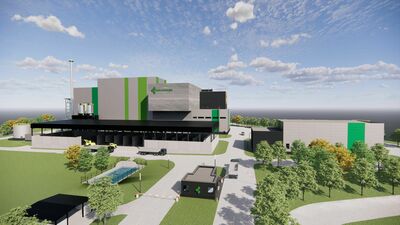
The plant will process 110,000 tonnes of refuse derived fuel per year in one line with an average calorific value of 12.5 MJ/kg. The thermal capacity of the incineration line is 48 MWth. The live steam, with a pressure of 65 bar and a temperature of 420°C, will be converted in a turbine/generator set into approximately 11 MWe of electricity and up to 31 MWth of heat, which will be supplied to MPEC's district heating network. Doosan Lentjes has supplied its proven water-cooled reciprocating grate system to ensure homogeneous incineration of the waste and to recover the energy contained in the waste. The plant also includes two gas/oil-fired peak load boilers for up to 70 MWth of district heating. The peak load boilers are already operational and supplying heat to the network.
The proven Circoclean® dry flue gas cleaning technology will absorb harmful pollutants such as sulphur dioxide (SO2), hydrogen chloride (HCl) and hydrogen fluoride (HF). Selective catalytic reduction (SCR) will ensure that nitrogen oxides (NOx) are reliably removed from the flue gas. The new plant will fully comply with the emission limits of the permit based on the latest EU BREF (Best Available Technique References) conclusions.
Furthermore, on-site treatment of grate ash from incineration contributes to recycling targets by recovering ferrous and non-ferrous metals. During several weeks of storage of the mineral fractions in a dedicated building, the remaining ash is aged and prepared for further treatment and possible recovery as construction material.
“The key to the success of the Olsztyn project is the synergy and cooperation between the international team members of Doosan Enerbility and Doosan Lentjes”, says Rafal Psik, Project Director Olsztyn. “There are many different nationalities represented in our team, which bring a lot of different competences and experiences. Of course, we are also aware that the waste-to-energy project in Olsztyn is very important for the local community: it will not only ensure a stable heat supply, but also provide more flexibility in waste management for the entire Warmia and Masuria region.”
Since thermal waste treatment is according to the European Waste Hierarchy the method of choice for the safe and environmentally sound disposal of non-recyclable and contaminated waste, the new waste-to-energy plant also fulfils an environmental task. It will also make an important contribution to saving climate-damaging CO2, as fewer fossil fuels will have to be used.
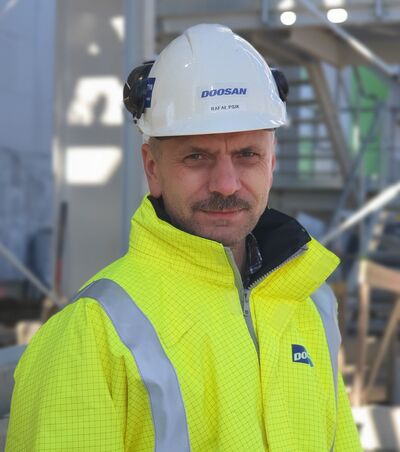
Warsaw plant under construction
In addition to Olsztyn, also the waste-to-energy plant in the Polish capital Warsaw is currently being realised with the participation of Doosan Lentjes. With an annual capacity of 265,000 tonnes, the plant will be the largest of its kind in Poland. Once completed, scheduled for 2024, after a construction period of 36 months, one third of the installed combustion capacity in Poland will be secured with Doosan Lentjes technology.
Poland needs more WtE
To ensure the country will meet the municipal landfill target of 10 per cent by 2035 of the European Green Deal, waste-to-energy is the go-to technology. But as of now, there are simply not enough facilities. In 2014 it was expected, that there will be up to 12 plants realized by 2020. This expectation has not been fulfilled.
The base of the Polish waste management concept is the pre-treatment by MBT (Mechanical Biological Treatment). However, the additional processing step produces approximately 30-40% combustible fraction while the major share of the introduced waste volume is still landfilled.
Assuming that the average plant size in the future will be 150,000 tonnes per year, the additional demand for waste-to-energy capacity in Poland can be estimated at a further 12-15 plants. In order to solve the Polish disposal problem for municipal waste and RDF and comply with the EU waste package's landfill target, further efforts must be made to increase the implementation speed for waste incineration projects.