Interview : “Our industry is facing major changes”
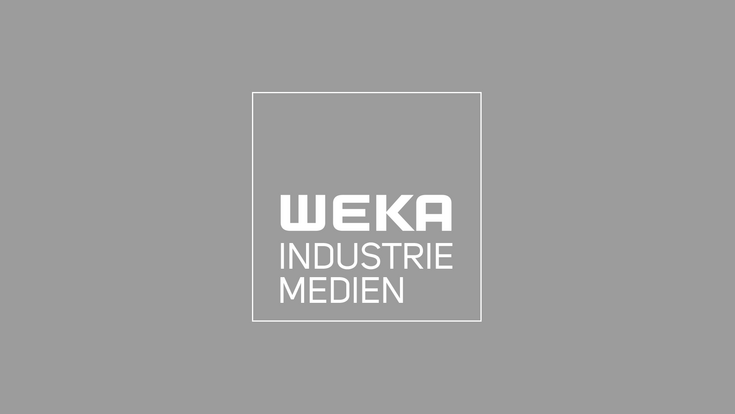
Mr Cibaldi, the increased recycling rates of aluminium present an opportunity for the whole industry. How has this changed Deral S.p.A.?
Mauro Cibaldi Over the last few years, we have been able to expand the range of incoming aluminium from the relatively high-quality scrap discarded from extrusion production cycles to more impure raw materials. Today we are able to include material from the demolition of windows and profiles in the melting cycle. This change has resulted in greater attention being paid to the quality of recycling and to the enhancement of the raw materials from scrap.
How did this process develop at Deral S.p.A.?
Cibaldi In 2015, this process saw the replacement of the old line with a first Flex 1000 mobile drum plant from Panizzolo complete with eddy current. Then, over the years, we have also implemented it with an X-ray selector that allows us to effectively identify and separate the secondary alloys from the primary aluminium ready for use. At Deral today, we are structured for a production of around 40-45,000 tonnes per year of finished product and we expect strong production growth over the next ten years.
Can you give us some numbers in terms of your staff and business?
Cibaldi We currently have 35 employees and five directors, and we occupy an area of about 28,000 square metres. This includes 4,000 square metres dedicated to production in a covered warehouse and 600 square metres of office space.
Your growth was made possible by an innovative treatment cycle in which Panizzolo Recycling Systems plays a key role. How does the Panizzolo system make your treatment cycle more efficient?
Pietro Giulio Vincoli When the business first started, we worked with shear presses and carried out the selection and cleaning phases manually. In particular, our doubleshaft shredder produced a very large piece of aluminium (50-60 cm) and forced us to slow down production. Furthermore, the quality of the product was not perfect, with clear repercussions at the time of casting. One of the first machines installed, due to timing reasons, was the Flex 1000 mobile drum, which started up in a very short time, while we have now switched to a stationary Mega 1100 hammer mill. Our first need was to increase the production capacity of the grinder and from the first accounts of the new production cycle we have already seen a clear improvement. With the grids set for our scrap, we have calculated a productivity of about 15 to 16 tonnes per hour.
What hourly productivity do you expect from the new plant?
Vincoli We will definitely produce at least 12 tonnes per hour, but since the recent startup we have already calculated that we are producing an average of 15 to 16 tonnes per hour.
What environmental policies do you apply at Deral S.p.A.?
Cibaldi We are certified under ISO 9001, ISO 14001 and also under Council Regulation (EU) No 333/2011, which certifies the transformation of our waste into secondary raw material. In addition, in December 2020 we received the environmental assertion validation certificate.
How do you think the sector will change in the coming years?
Vincoli Major changes are taking place in our industry. Over the next 10 to 15 years, there will be an increasing number of structured companies with complete systems that will carry out the total enhancement of the material in-house. In this process, the figure of the simple scrap dealer will disappear. In order to face the near future, companies must therefore structure or deconstruct themselves. An example? As a foundry, we collect demolition material or ready-made material; there is no longer any middle ground.
Cibaldi At a European and national level, a whole series of incentives are flourishing for products and materials that have particular value within the circular economy. Among these materials, aluminium plays one of the most important roles. Aluminium is 100% recyclable, with its recycling process requiring 1/20th of the energy that would be used starting from the raw material. It is being used to an ever-increasing extent due to its lightness and strength, and it emits very little CO2 during melting. All these are elements on which we are focusing heavily and they will ensure that aluminium becomes the material of the near future.
And how will this change Deral?
Vincoli At Deral, thanks to the very strong demand for aluminium and the regulations aimed at reducing CO2, we are considering making an additional investment in the treatment plant. For this reason, I think that the 1100 Mega Panizzolo shredder has considerable chances of success for the treatment of aluminium. With the same machine, it is possible to work both the profile and the casing and also other types of aluminium. However, it remains a low-cost machine of a decent size.