Baler Integrated with Conveyer Which Survived Fire in One Day : Refurbished Waste Baler from Middleton Helps GHS Recycling Recover from Fire
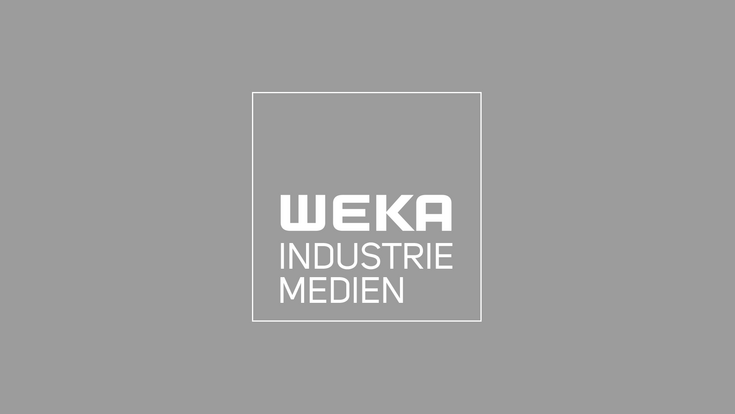
Glastonbury, UK based recycling machinery specialist Middleton Engineering, has helped put Portsmouth based GHS Recycling back on its feet following a disastrous fire with the installation of a refurbished closed-end semi-automatic baler.
The fire which struck in September 2016, destroying a £70,000 baling machine and a storage area for processed waste, almost spelt the end for the 30 year old family firm. The replacement baling machine was supplied at short notice and installed in a day.
However, five months on the business said that it is stronger and tonnage is up thanks in part to the new machine and the support of its customers.
For hands on general manager Rachael Harris and her brother James Harris, who operate the business started by their father, the fire was a sobering experience.
Managing waste volumes of 100 tonnes a week, the company helps customers divert waste from landfill, collecting and processing a range of materials including confidential waste, paper, card and plastics from businesses of all sizes.
Middleton explained that for GHS replacing the lost baler was an immediate concern if the business was to continue functioning. To do so it would need to interface with an existing conveyor which fortunately had been salvaged from the fire with some cosmetic damage and blistered paint. It was repainted by Rachael and GHS the team.
However, the company added that it was also an opportunity to source a machine that would deliver the bale weights and dimensions necessary to optimise trailer loads - a major cost for the industry - something that the previous machine had failed to do.
“We needed a quick solution. It would have to be a stop gap and unfortunately new wasn’t an option, but it was also an opportunity to source a machine that would allow us to achieve maximum weight for the bales we were producing and improve throughput,” explained Rachel.
Following recommendations and a site visit to assess GHS’s needs, Middleton Engineering installed the refurbished baler, an ME 80 semi-automatic baler capable of delivering consistent mill size bales with a press force of 80 tonnes. The high pressure is said to enable compact bales to be achieved reducing transportation costs, at the same time working well with all waste streams.
According to Middleton a key challenge was integrating the machine with the existing conveyor, which needed to be repositioned in a space that was still being cleaned up after the fire.
Rachael added: “Middletons responded rapidly and got on with job efficiently, going the extra mile to reposition and integrate the existing conveyor.”
“The experience has made us more resilient,” she concluded. “Customers have been extremely loyal and with the new machine we are now achieving maximum tonnage in terms of bale size and weight. Before this we were sending out artics only partially filled and down on weight, but now we are more competitive which in turn means we can deliver improved rebates to our customers too.”
Read More
‘World First’ rHDPE Plastic Recycling Facility in Redcar Upgraded by Middleton Engineering
Middleton Engineering, has installed a second bespoke conveyor to enhance processing requirements at Biffa Polymers, food grade High Density Polyethylene (rHDPE) recycling plant in Redcar, Cleveland.
Middleton Engineering’s Turnkey Solution for Small Scale Welsh Recycling Facility
Middleton Engineering, has completed a new 5000 tonne per year Materials Recycling Facility (MRF) for Merthyr Tydfil County Borough Council.
Middleton Baler Processing RDF for Island Waste on Guernsey
Guernsey based waste and recycling firm, Island Waste, has become the first on the Channel Island to process and ship RDF off island, following the installation of a new twin ram baler and conveyor solution from Middleton Engineering.