Consumer Goods Firm Partners with TOMRA, Veolia, SUEZ, RECOUP and Viridor : Unilever to Roll Out Pigment to Increase Recycling of Black Plastic HDPE Packaging
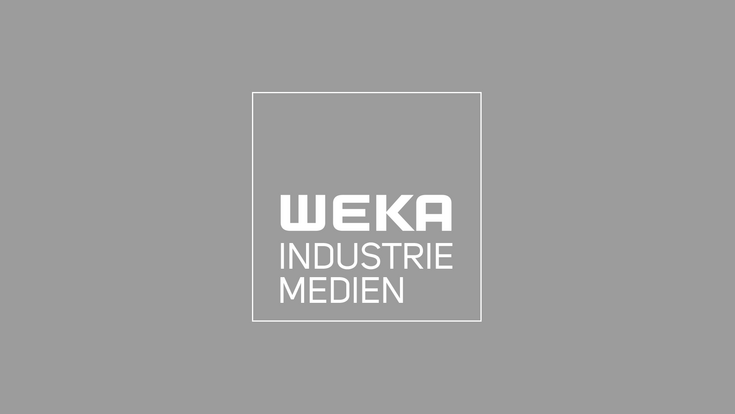
Anglo-Dutch Consumer goods giant, Unilever, is to phase in the use of a new detectable black pigment for its High Density Polyethelyne (HDPE) bottles for its brands, TRESemmé and Lynx, so they can be detected by recycling plant scanners and sorted for recycling.
This means that around a further 2500 tonnes of plastic bottles could now potentially be sorted and sent for recycling each year.
The new detectable bottles will be phased in during 2019 and will allow Unilever to further ‘close the loop’ and include the recycled black plastic back in new packaging. In 2019, TRESemmé and Lynx will both introduce a minimum of 30% recycled material into their packs.
Currently ‘standard’ black plastic bottles go undetected by the automatic optical sorting machines in recycling plants because they use near infra-red light, which is absorbed by the ‘carbon black’ pigment traditionally used to colour them. This effectively makes them invisible to the sorter and leads to them being rejected and sent for waste.
Unilever has carried out extensive trials, in partnership with RECOUP and waste management partners Veolia, SUEZ, Viridor and TOMRA, which have proven that this new pigment can be technically detected within their material recycling facilities in the UK.
Unilever said that the knowledge and expertise from developing this technical solution for detectable black bottles will be made accessible to others in the industry, as well as to other markets globally: “We will be pleased to share our work and the insights generated with other manufacturers to enable wide use of this technology and approach.”
Unilever’s solution will enable TRESemmé and Lynx bottles to be detected by recycling scanners, with minor adjustments at the material recycling facilities, so they can be technically separated, sorted and sent for recycling, becoming a useful resource rather than ending up as waste.
This move to using the new detectable black plastic is part of Unilever UK’s commitment to The UK Plastics Pact and its new ‘Get Plastic Wise’ campaign, a Five Point Plastics Plan which aims to tackle plastic waste in
the UK and move towards a closed loop where plastic stays within the plastic economy, not the environment.
Sebastian Munden, General Manager of Unilever UKI, said: “We’ve been working on a solution for black plastic for some time, and this move to using detectable black plastic in our TRESemmé and Lynx bottles means we will potentially be removing around 2,500 tonnes of plastic from the waste stream.
“Unilever has committed to ensuring that, globally, all of our plastic packaging is fully reusable, recyclable or compostable by 2025, and to using more recycled plastic content in our packaging. For the UK & Ireland we want to significantly accelerate this and we’re proud our innovation will help us towards achieving our aim, as well as making a significant contribution towards the UK Plastics Pact targets. We’d like to thank our industry partners for their part in working with us to make this possible.”
Richard Kirkman, Chief Technology and Innovation Officer at Veolia UK & Ireland added: “Black plastic bottles were invisible to our machines but in collaboration with Unilever we have upgraded the technology to accept "detectable black" - if a bottle is marked as 'detectable' then it can come to a Veolia MRF and will be recovered.
Recycling is a chain of events from manufacturer, consumer to recycler and we need each part of the chain to make changes to have successful scalable results.
“We have deployed an innovative solution within the software and invested in our sorting technology at our flagship recycling facility in Southwark and this, together with Unilever modifying the pigment in the black dye for their HDPE packaging, enables it to be successfully detected. If all recyclers and manufacturers follow this means black plastic becomes detectable black.
“Adjusting the detection mechanism in this way - with both technology and packaging modified was the key. It’s the first time a hi-tech solution like this has been applied to black plastics and can be rolled out at scale - a eureka moment for recycling and a rallying call for similar partnerships to take shape. This is exactly the kind of thing the Plastics Pact was set up for and its inspiring a generation of engineers.”
Helen Bird, Strategic Engagement Manager at WRAP, which manages The UK Plastics Pact, commented: “Tackling plastic waste is complex and involves collaboration across the supply chain. We welcome this move by Unilever and steps taken by waste management companies to trial the sorting of the packaging. We now call for wide scale adoption of detectable black pigments by brands and retailers, and the sorting and reprocessing of that packaging by the recycling sector.”
Stuart Foster, CEO, RECOUP said: “Through the commitment and leadership of Unilever, and with the support of the resource management industry, this is a fantastic example of how detectable pigments can be used to improve plastic packaging sortability and recyclability and shows what can be achieved through practical partnerships and real cross supply chain collaboration.
“Unsortable plastics, particularly the traditional carbon black packaging, has been one of the key interest areas for media, consumers and politicians in recent years. The sharing of data, knowledge and solutions was the focus of the RECOUP led Black Plastic Packaging Recycling Forum, and we encourage all manufacturers, brands and retailers to follow the leadership of companies, such as Unilever, and ensure that plastic packaging placed on the market can be recycled.
Phil Piddington, Viridor’s Managing Director, said: “As a founding member of The UK Plastics Pact, Viridor is committed to working with all sectors to achieve greater recyclability in the design of packaging and products. This allows us to maximise the volumes recycled and contribute to a more resource-efficient UK.
“The collaboration with Unilever – which saw the HDPE bottles trialled at Rochester Polymers Recycling Facility - was an excellent example of how sectors could work together to help the UK achieve its circular economy ambitions.
“We are pleased to work with Unilever on a project which supports recycling efforts at the kerbside by offering closed loop recycling solutions, reducing the use of virgin plastic and giving the public increased confidence in recycling and reprocessing here in the UK.”
Stuart Hayward-Higham, Technical Development Director at SUEZ added: “We have welcomed the general reduction in the use of unnecessary black plastics placed on the market but recognise the responsible lead Unilever has taken in seeking to create a closed loop solution for their black plastic products, including the design and testing of detectable black plastic polymers. In collaborating, the value chain is starting to show what is possible.
"We look forward to continuing to work on this project to see how these materials can successfully be collected, sorted and recycled into new Unilever products within the existing or future mainstream waste management systems.”
Jürgen Priesters, VP and Head of Business Development at TOMRA Sorting Recycling commented: “Currently, not all plastic items are sortable and recyclable and therefore go on to be incinerated or in landfill sites, including carbon black products.
"Carbon black plastic materials are not detectable with standard NIR (near infrared recognition), which is used in most modern sorting plants worldwide. As carbon black plastic packaging items account for 3-6% of all plastic packaging products, we are talking about a significant amount of material not being recycled today.
“Unilever has successfully developed black PE (Polyethylene) plastic packaging items which are easily detectable with standard NIR units used around the world. This material was successfully tested several times and approved in the TOMRA Sorting GmbH test facility.
“With this development, Unilever has set a new standard that will massively increase recyclability without requiring existing sorting plants to invest billions of Euro in technology. We do hope that others will follow such an innovative development and help all of us to achieve much higher, better recycling figures than today.”
Read More
TOMRA E-Book – Technically Possible to Produce Goods from 100% Recycled Plastics
TOMRA Sorting Recycling has published an e-book which it said shows that it is technically possible and economically worthwhile to produce goods from 100% recycled plastic.
COMMENT: Keep It Simple When it Comes to Kerbside Recycling Collections
Richard McKinlay, Axion’s Head of Circular Economy, has called for residential kerbside recycling collections tp focus on consistent quality if the UK is to boost plastics recycling rates and meet current targets.