Industrial Waste : Dekasan safely processes hazardous waste with WEIMA shredder for RDF
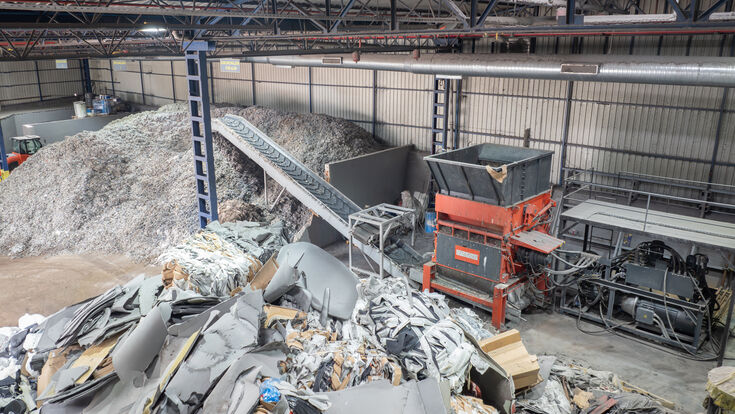
Shredding process for household and industrial waste at Dekasan.
- © WEIMAThe Turkish company Dekasan has been providing waste management services since 1982. Located in the Kayapa Industrial Zone in Bursa, western Turkey, Dekasan collects, separates or recycles more than 20,000 tonnes of household and industrial waste each year. In April 2024, the company expanded its operations by introducing a processing line for hazardous waste from industrial processes. Waste from rubber, plastics, textiles, chemicals, paint products and containers contaminated with toxic substances are converted into refuse derived fuel (RDF) using a WEIMA PowerLine 2000 shredder. The high calorific value RDF is then sold to cement manufacturers in the region.
Throughput of up to 9 tons per hour
The waste is delivered by truck and fed into the shredder via a gripper. The PowerLine 2000 shredder, equipped with a 315 kW hydraulic drive from Hägglunds Bosch Rexroth, reduces the material to a uniform particle size of 50 mm. With a working width of 2,000 mm and a rotor diameter of 800 mm, the PowerLine series is ideally suited for single-stage shredding of various waste types. The robust construction of the WEIMA shredder excels under these fluctuating material streams and demanding conditions.
“Depending on the material, we achieve throughput rates of four to nine tons per hour,” explains Environmental Engineer Tolga Boşnak, who was responsible for acquiring the shredder and establishing the new RDF line
Improved working conditions through dust reduction
Dekasan also installed an injection system to wet the material in the hopper area during the shredding process. This results in a significant reduction in dust in the production hall, creating a safer and more comfortable working environment for employees.
Safe processing and quality control in an in-house laboratory
The shredded material is transported on a belt and passes through a metal separator. Before transport, Dekasan carries out a chemical analysis of the shredded material in its own laboratory. Depending on customer specifications, the calorific value can be adjusted by mixing different batches.
Reliable operation with intelligent shutdown
Industrial and hazardous waste is not only particularly abrasive and difficult to shred, it often contains interfering materials such as metal. If these materials enter the shredder, it automatically shuts down. The hydraulic inspection flap makes it easy to remove the materials and restart the machine quickly, reducing downtime.
Service agreement ensures continuous performance
To further minimize downtime, Tolga Boşnak opted for a service agreement with WEIMA. Quarterly, a WEIMA technician inspects the shredder thoroughly. In addition, adjustment parameters can be remotely configured as needed.
One shredder, many advantages
The decision to purchase a WEIMA shredder was based on several factors. In contrast to other offers, WEIMA was able to handle the required task with a single shredder instead of a pre-and post-shredding system. This not only saves space in the production hall but also reduces purchase and maintenance costs. In addition, the robust hydraulic drive with its variable speed range, the machine's reliability and the service offered were decisive factors.
"We have been very satisfied with the machine from the start and we look forward to installing more WEIMA shredders and machines in our facilities and to a long-term partnership," says Tolga Boşnak.