Plastic Waste : Doğa PET takes PET recycling quality to new level using TOMRA
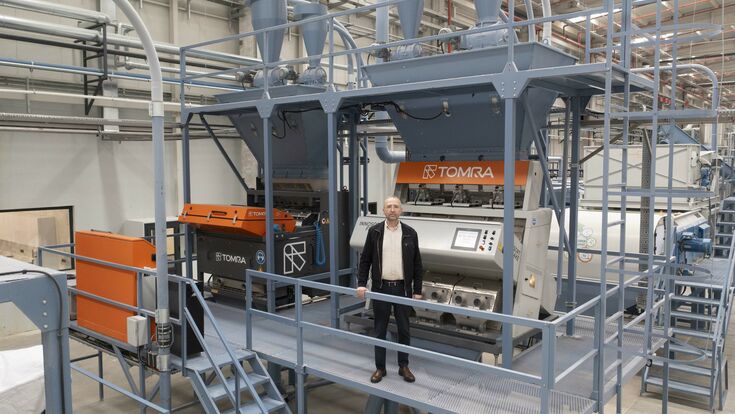
Dr. Gerlikhan: "For us, using TOMRA's state-of-the-art sorting systems is crucial.”
- © TOMRAAs Türkiye continues to expand its environmental and industrial sustainability agenda, Doğa Holding—one of the country’s leading conglomerates—has made a notable move into the recycling sector. Its latest venture, Doğa PET, is rapidly becoming a key player in post-consumer PET recycling, with an ambitious focus on delivering food-grade and textile-grade recycled materials. The company’s success so far hinges on a strategic partnership with TOMRA Recycling, whose advanced sensor-based sorting systems are driving both efficiency and quality at the new facility.
Building a world-class recycling operation
Strategically located in northwestern Türkiye, the Doğa PET facility currently processes over 4,200 tons of post-consumer PET bottles each month. From this, it produces approximately 1,000 tons of premium PET flakes and 2,000 tons of rPET granules monthly. These outputs are carefully tailored for demanding applications in food packaging and the textile sector—markets where consistency and purity are non-negotiable.
Doğa PET has outfitted its operations with TOMRA’s full suite of plastics sorting technologies, including four AUTOSORT™ units, two INNOSORT™ FLAKE systems, and two AUTOSORT™ FLAKE units. This comprehensive configuration ensures precision sorting at every stage—from bottle pre-sorting through to final flake purification.
“The plant’s production line features four AUTOSORT™ units which pre-sort the PET bottles,” explains Serkan Orhan, Sales Manager for TOMRA Recycling Sorting in Türkiye and the Middle East. “The first three sort by material and color before sending them to the subsequent crushing and washing line. The fourth AUTOSORT™ unit re-sorts the rejected products from the first three units, sending recoverable materials back to the first AUTOSORT™ to improve efficiency and material recovery.”
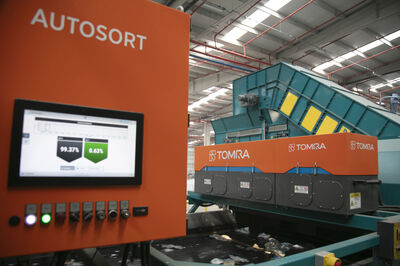
Following this initial sorting, the material undergoes a full wash and drying cycle before advanced color and polymer sorting begins. “Finally, the flakes are sent to the AUTOSORT™ FLAKE unit,” Orhan adds, “a specialist solution for high-end flake sorting applications such as food-grade bottle-to-bottle recycling. At this sorting stage, the targeted high purity is achieved thanks to the reliable separation of color, polymer and metal contaminants.”
Precision sorting, premium output
Doğa PET’s commitment to quality extends beyond machinery. Dr. Selçuk Gökhan Gerlikhan, General Manager of Doğa PET, highlights how TOMRA’s technology has helped the facility meet ambitious purity benchmarks.
“We separate purity levels into two categories: polymer and color,” says Dr. Gerlikhan. “Our target for polymer purity was 99.998% for the final product, and we achieved this. For color, our goal was to reach a purity level of 99% transparent PET in the final product. This includes reducing other colors, such as light blue PET, to below 1%. We have already exceeded expectations by achieving color variations below 0.5%.”
Doğa PET is also pioneering color separation in Türkiye. It is the first domestic facility to successfully distinguish and isolate light blue PET from clear PET—regardless of the composition of the infeed material. This allows the company to recover the light blue fraction separately, maximizing resource use and opening up additional applications for this recovered material.

Smart monitoring for regulatory assurance
Beyond purity, Doğa PET is investing in digital tools that support compliance with food-grade recycling regulations. The plant uses a high-tech waste analyzer powered by PolyPerception, which monitors material quality in real-time via camera systems. Positioned before the final AUTOSORT™ unit, this analyzer ensures that less than 5% of incoming material is non-food grade PET—an essential threshold for producing certified food-grade rPET.
The analyzer also provides shift-based data tracking, enabling Doğa PET to deliver batch-specific quality documentation. This level of transparency is critical for European export markets, where regulatory and customer standards are especially stringent.
A dual focus: bottles and textiles
While much of the industry focus remains on bottle-to-bottle recycling, Doğa PET is also targeting the textile sector, which places equally demanding requirements on rPET quality.
“The filament sector in textiles demands very high purity levels and color stability,” says Dr. Gerlikhan. “The durability, aesthetics and functionality of the final fiber product depend heavily on the proper management of the PET recycling process when producing high-quality rPET granules.”
To meet these standards, the company relies heavily on TOMRA’s sorting solutions to maintain consistent granule characteristics—critical for the production of high-performance synthetic fibers.
Looking ahead
With plans to expand and scale up its recycling lines further, Doğa PET is poised to become a cornerstone of Türkiye’s circular economy. The facility’s advanced setup demonstrates what’s possible when industrial ambition meets technological precision.
Serkan Orhan of TOMRA concludes: “We are delighted to have been by Doğa's side from the very beginning on this project. Achieving the desired capacity and quality levels in such a short period of time with such vast inputs has been a great achievement which demonstrates how advanced sorting technology contributes to achieving virgin-like material qualities."
In a region where modern recycling infrastructure is still emerging, Doğa PET stands as a model for how innovation, investment, and collaboration can turn waste into high-value resources—setting a new bar for PET recycling in Türkiye and beyond.