Recycling : HML Recycling Operate Bunting Magnetic Separators
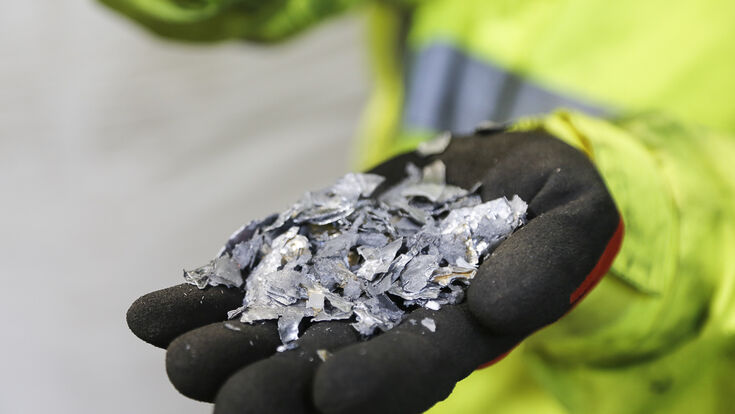
Shredded perfume bottle tops
- © Paul Fears PhotographyEffective metal separation is one of many important processes in HML Recycling’s specialist metal recycling operation in Accrington, UK. HML has installed Bunting Permanent Overband Magnets in their cable recycling process, and a Metal Separation Module on a new line for recycling perfume bottle tops.
Bunting is one of the world’s leading designers and manufacturers of magnetic separators, eddy current separators, metal detectors and electrostatic separators. The Bunting European manufacturing facilities are in Redditch, just outside Birmingham, and Berkhamsted, both in the United Kingdom.
HML Recycling has over 50 years of experience in metal recycling and works with local people and multinational organisations to implement effective metal recycling solutions. The company sponsors many local charities, sporting clubs and community projects and pledges a percentage of operating profits to worthy causes each year.
HML recycle a wide range of metals including an established cable recycling plant and a new line for handling shredded perfume bottle tops. On the cable recycling plant, HML use two Permanent Overband Magnets to remove ferrous metals including steel after primary shredding. One Overband Magnet is positioned across a vibratory feeder, where the vibration liberates entrapped material to enable to cleaner separation of magnetic metals. The second Overband Magnet removes steel and other magnetic metals from a 98%-rich shredded copper cable mix to protect a granulator. Mounted above the granulator feed conveyor handling up, the Overband Magnet lifts and removes potentially damaging steel.
HML have recently installed a new line for the recycling of shredded perfume bottle tops. The mix includes both ferrous and non-ferrous metals, which are removed using a Bunting Metal Separation Module. In operation, the shredded material is fed via a conveyor onto a Vibratory Feeder. The Feeder evenly spreads the material before feeding at a steady rate onto a high-strength Permanent Drum Magnet, which separates any magnetic material. A Drum Magnet has a fixed magnet element mounted inside a rotating non-magnetic shell. Any ferrous metal or magnetic particle is attracted and held to the surface of the rotating Drum Magnet shell before being transported and deposited underneath in a collection area.
The remaining non-magnetic mix drops onto the moving belt of a High-Intensity Eccentric (HIE) Eddy Current Separator. An Eddy Current Separator is a dual pulley conveyor system, where the non-metallic rotor cover houses an independently rotating high-speed magnetic rotor. Separation occurs when a non-ferrous metal particle (e.g. aluminium) is conveyed into the magnetic zone. The non-ferrous metal particle is exposed to rapidly changing magnetic polarity. This induces ‘eddy currents’ into the particle generating an electrical current (Fleming’s left-hand rule) that subsequently creates its own magnetic field. The two magnetic fields oppose each other (i.e. North vs North pole repulsion), causing the repulsion of the non-ferrous metal particle and change in trajectory. The measured positioning of a splitter enables the separation of non-ferrous metals from non-metallic material due to the altered and unaltered material trajectories.
Prior to ordering the magnetic separators, Bunting conducted control tests at their Customer Experience Centre in Redditch, UK to confirm capacities and separation capabilities. In operation, the 750mm wide Drum Magnet and Eddy Current Separator will handle up to 2 tph of 0-15mm shredded perfume bottle tops. Both the recovered aluminium and plastic will have purities exceeding 98%.
“The HML Recycling installation is another exciting project for Bunting,” said Tom Higginbottom, Bunting’s Sales Engineer. “Conducting the tests at our Customer Experience Centre enabled us to understand the material and ensure that we could meet the separation expectations.”