Sirmax Group presents GAPP technology at K 2022 : Sirmax: Injection molding without weld lines
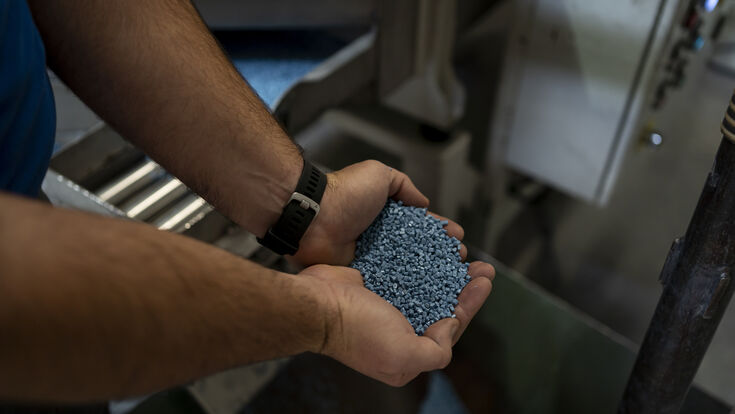
Based in Italy, Sirmax Group is among the world's leading producers of thermoplastic granulates for all sectors of use – automotive, home appliance, power tools and household, electrical, electronics, construction, and furniture. The group will be at the 2022 edition of K with many developments resulting from investments made by the group in the last three years, despite the pandemic and geo-economic events. Sirmax is a global company able to offer its products and technology equally in all parts of the world thanks to 13 factories and 5 R&D centers.
“2022 has been an intense year for Sirmax. We have never stopped innovating, despite what has happened in the world and the repercussions on the global economy,” says Massimo Pavin, Sirmax Group President and CEO. “We are proud to bring our innovations and our sustainability model – which for us means, above all, investing in all phases of the production process and involving the most prestigious universities in the world – to K 2022. Thanks to our expertise and scientific approach, we are able to offer upcycling solutions that reduce CO2 emissions and maintain very high performance. Our goal is to be even closer to our clients, with a view to true proximity compounding.”
No more weld lines with Gas-Assisted Push Pull (GAPP) technology
GAPP technology is an innovation that allows for the injection molding of thermoplastic material without weld lines. Through Smart Mold, a university spin-off 50% owned by Sirmax, the group has developed an innovative system that avoids weld lines in plastic products, saving time and costs for the client. Sirmax Group will present GAPP on Thursday, Oct. 20, starting at 5 p.m., at booth C69, Hall 8B. The presentation, with Professor Giovanni Lucchetta of the University of Padua, will be followed by a drinks reception starting at 5:30 p.m.
GAPP promotes the interpenetration of weld line flow fronts in a way that changes the shape of the interface, promotes inter-diffusion between flow fronts, and realigns reinforcing fibers. Weld lines are among the most critical structural defects in parts made by the injection molding of fiber-reinforced thermoplastics. In a weld line, reinforcement fibers adopt an orthogonal orientation with respect to the filling direction, which results in a significant reduction in the strength and rigidity of the molded part, adversely affecting its structural performance.
Experimental tests have shown that GAPP can increase weld line strength by 240% in polypropylene reinforced with 35% short glass fibers, almost reaching the nominal strength of the compound.
The launch of the E-commerce platform
GAPP technology joins the other innovative initiatives that Sirmax Group is launching to give its clients customized products that are increasingly aligned to their needs. With this in mind, the group is launching an E-commerce platform developed entirely by Sirmax which allows the group's clients to place new orders and have a complete view of all documentation related to their order history. By making all technical documents available, Sirmax facilitates the supplier/client relationship. The E-commerce platform will also be used to promote the group's main products. In addition, a ‘convenience corner’ will offer a range of in-stock materials at an affordable price. The E-commerce platform is already active internationally and accessible via the link on Sirmax’s official website, www.sirmax.com. Restricted features can be activated on invitation by the Sirmax team.
The group's 14th plant, and 3rd in the US, is on the horizon
Sirmax Group also continues to invest in its production infrastructure. The Anderson site (Indiana, USA), which now has two plants, will be upgraded and expanded by 2025. The first plant will house thermoplastic elastomer production and a new warehouse, increasing the total production area from 13,000 to 26,000 square meters. The site’s 10-year development plan also involves enhancing recycled compound production, expanding the production area from 11,000 to 27,000 square meters, and building a third plant of around 12,000 square meters for the production of engineering plastics.
“This is a 10-year project involving investments of around $200 million and has the potential to triple current production capacity,” explains Lorenzo Ferro, Country Manager of Sirmax North America. “In Indiana, our goal is to develop a large hub capable of serving the entire US and Mexican markets in line with Sirmax group's multi-region and multi-product strategy. This would involve implementing the production of all business lines in the Anderson industrial park.”
A richer website and an innovative exhibition booth
On the communication front, Sirmax has revamped and enriched its official website, adding German pages as well as the E-commerce platform. In addition, Smart Mold – the spin-off that Sirmax Group acquired 50% of in 2020 – now has its own dedicated website, which includes descriptions and specifications of the engineering and technology services it offers. Smart Mold specializes in product, mold and process engineering; the structural and process simulation of plastic parts; the substitution of metal for plastic; the characterization of materials for structural and process simulation; and process analysis and troubleshooting. The site can be accessed through the Innovation page of Sirmax’s official website or from www.smart-mold.it.
Innovation also comes through visual communication and new ways to convey the values of sustainability. At K 2022 in Düsseldorf, Sirmax Group is presenting a brand new corporate video that dynamically and creatively explains the group's approach to sustainability, as well as a 3D-printed model which will be at the Sirmax booth for the duration of the event. Visitors will be able to see and touch all the stages of the upcycling process that Sirmax implements as part of the circular economy to create innovative and sustainable materials. The model shows how we sort, wash, and elevate materials through recycled plastic compounding